Going Paperless with Descartes Heightens Delivery Performance for Customers
As a wholesale distributor of building materials serving 12 states with 60 locations, Homer Glen, IL-based Richards Building Supply (RBS) invested in route planning and delivery software to help ensure consistent, on-time delivery to its growing customer base.
Using Descartes’ route planning, execution and mobile solution, the company has been able to automate delivery route planning, and proof-of-delivery (POD) to heighten the delivery experience and improve delivery performance—especially critical during the peak summer season.
Real-time Delivery Route Planning
Contractors’ delivery expectations have changed. Lead times on orders are often less than 24 hours. Some orders need to go out the same day, and others need to adhere to specific delivery time windows.
By replacing traditional paper-based route planning with route planning technology, RBS can now plan deliveries, optimize routes, and communicate with drivers and customers in a completely paperless environment. With more intelligent route planning, RBS has improved on-time delivery performance.
"The new Richards Building Supply proof-of-delivery is great for our business. It assures us that materials were delivered in a timely fashion and provides reassurance that, when my crew shows up to the job site, all materials are there and ready for them to begin the project. Great addition to an already exceptional customer-service based company."
– Eric Shaffer, Archway Restoration
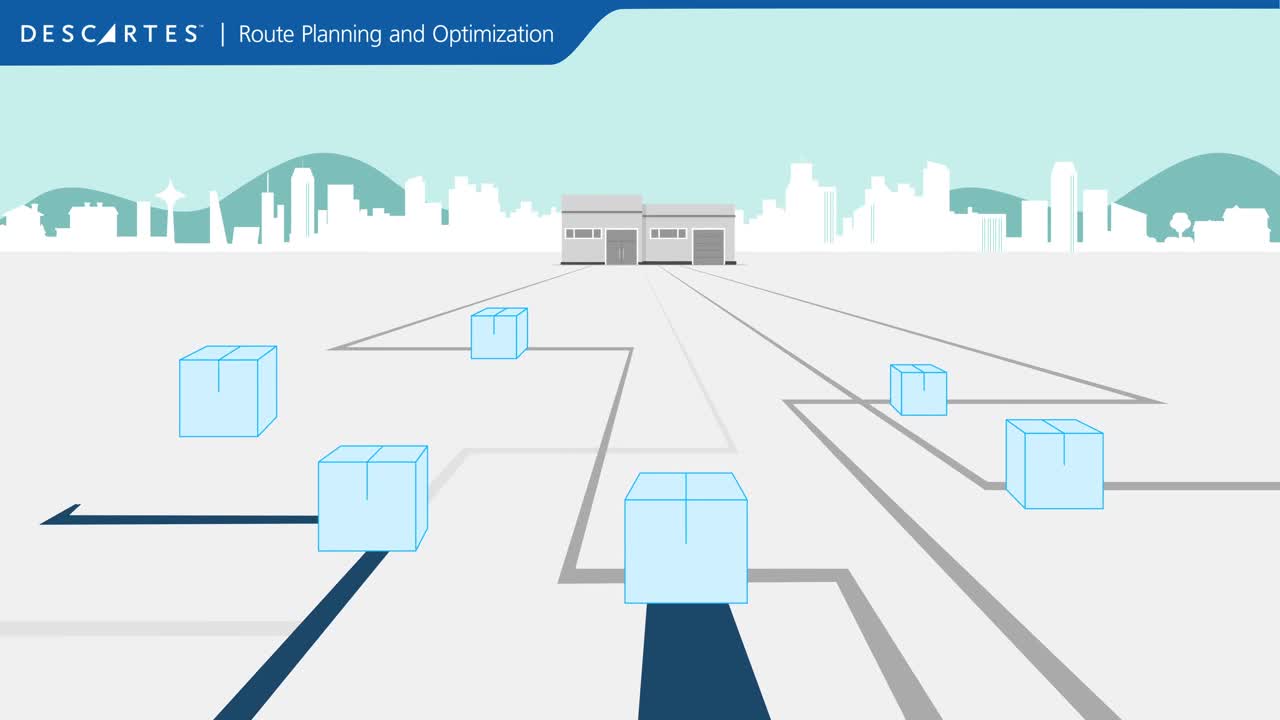
Real-time Updates on Mobile Devices
Richards’ drivers access delivery schedules using a mobile device. GPS information is received every few minutes to provide RBS with full visibility into vehicle locations to monitor delivery times against customer expectations.
With mobile technology, contractors also know exactly what material has arrived and when so they can keep construction projects on track. Communications can be received via email and/or text messages (standard text message rates may apply).
Paperless Proof of Delivery
Paper-based proof of delivery is fraught with illegible details and lost paperwork. With mobile devices, Richards’ drivers now use digital pictures to verify that the right materials, in the right quantities, in the right condition, were delivered at the right place and time.
It gets drivers back on the road quicker to meet other delivery time windows and helps drive up the number of deliveries per day.
With last mile delivery technology, RBS has improved coordination of the many variables involved in delivery: customer requirements, material and vehicle requirements, map data, scheduling, and delivery parameters and more.
INDUSTRY WHITE PAPER
Dynamic Route Planning Can Dramatically Improve Productivity
Download the white paper to see how fleet operators can show the value that dynamic route planning software can bring to the bottom line.
Making Last Mile Delivery a Priority
RBS is deploying the route planning software on a branch-by-branch basis throughout its operations. The Descartes solution combines scheduling, delivery route planning and execution, proof-of-delivery, automated pre- and post-delivery notification services, and imaging functionality into a comprehensive platform that can transform distribution operations.
"With the Descartes solution, we now have real-time visibility into deliveries as they are made—and proof of delivery when customers receive their orders," explains Nicholas Chesna, Fleet Assistant Manager, RBS. "We are in a much stronger position to drive realistic and reliable delivery schedules, increase the number of deliveries we can make each day, and ensure delivery time windows are tightly coordinated with customer requirements."
Real-time updates from GPS-tracked vehicles provides visibility into driver availability, the status of deliveries throughout the day and the ability to notify customers of delivery progress. "It’s far easier to keep customers informed during the day and we can easily change orders if needed. This has been instrumental to us and to our customers when weather interferes with planned work and the associated planned deliveries."
By optimizing scheduling and delivery processes, RBS is also getting more capacity out of its vehicles. "We can better manage customer orders for our diverse product mix in vehicles of appropriate sizes and with appropriate capabilities," notes Chesna.
By ensuring the right product is loaded onto the right truck—and unloaded properly at the job site—the solution is also helping RBS to reduce the number of delivery challenges. "Going paperless for delivery has been a win for our company and, more importantly, for our customers."
By implementing technology that helps the company run more efficiently while better serving customers, RBS has enhanced on-time delivery performance for commercial and residential customers alike.
Download the Success Story
Richards Building Supply
Fleet Resource Center
Expand Your Routing, Mobile & Telematics Knowledge
Recommended For You


