Whilst a great deal is made of the potential opportunities afforded by Freeports in the UK, many do not realise they can already achieve many of the customs benefits now. One such opportunity is using Customs Warehousing.
A common problem companies want to solve is paying the right amount of duty at the right time and not paying more duty than they must. Customs Warehousing provides an answer to that problem.
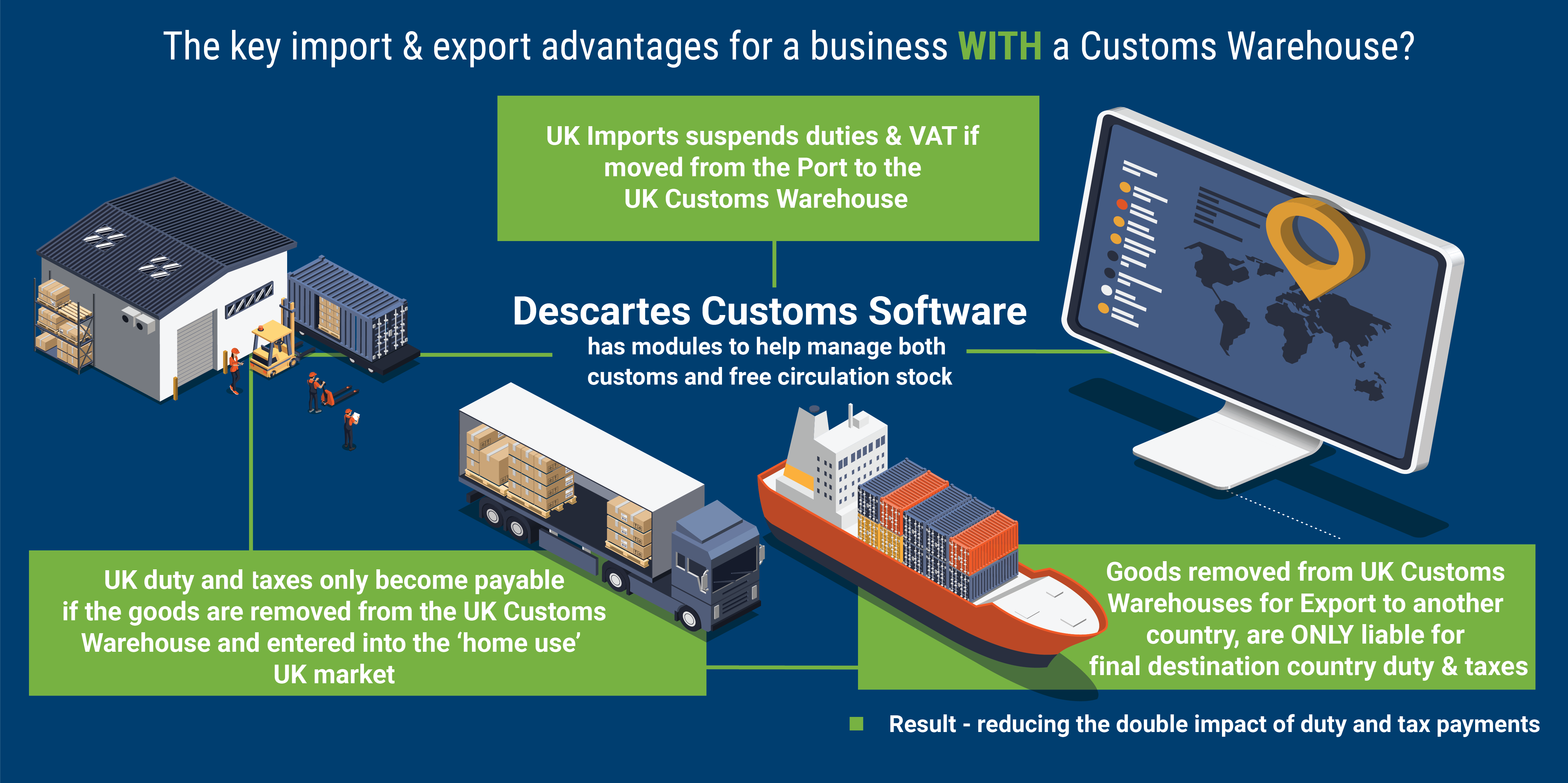
Strategic Export Planning: Avoiding Double Duties
The key benefit of Customs Warehousing is that goods can be stored indefinitely (providing it is safe to do so) without payment of duties or taxes. This is of particular benefit in two specific scenarios:
- The goods may be stored for a significant period of time that the cash flow benefit of deferring payment of duty exceeds that which could be achieved by simple use of a deferment account.
- The goods will eventually be re-exported from the UK, thus avoiding paying duty twice, once into the UK and again on entry into the export market.
The fact that it is possible to operate online retail sales using a bonded warehouse, where goods are picked and dispatched to order, is a big benefit for ecommerce.
This is particularly important as just storing goods does not change their origin, so it would not be possible to claim preferential duty rates into the export market unless some specific arrangements had been made between the UK and the export market to recognise a third country origin for the purposes of reduced duty rates.
EU Trade Continuity: Retaining EU Status with Customs Warehousing
Another key benefit related to this clarification from UK Customs is that goods stored in Customs Warehousing can retain their EU Status for up to 5 years (6 months in the case of goods falling within Chapters 1 to 24 of the Tariff). This should mean that goods placed into Customs Warehousing could be re-exported under a T2 movement and re-enter the EU under T2 Transit procedures, which is potentially easier than claiming Returned Goods Relief back into the EU.
However, there are some important additional caveats to note:
- The goods must have arrived under the T2 NCTS Transit procedure, although there does not need to have been an intention to re-export at the time of receipt.
- The details of the T2 must be held and quoted on the subsequent movement and so by logic equivalence cannot be used and the goods must move back to the EU under T2 NCTS Transit procedures.
- The goods cannot have been processed other than that needed for their preservation in their original state, or for splitting up consignments without replacing the packaging.
Whilst in warehousing it is also possible to perform sampling handling operations or move the goods to inward processing.
Inward Processing, also available on its own, benefits traders who import goods for processing (manufacturing or repair) and then re-export the goods by suspending the duty which only becomes payable if the goods remain in the UK. It is important to check any Free Trade Agreements to see if processing under duty suspension disqualifies the finished product from obtaining reduced duty rates into the export market, in which case a judgement has to be made which is better: paying UK duty or the Duty in the country of destination.

HMRC Approval Process: Navigating Regulatory Requirements
Both Customs Warehousing and Inward Processing require prior approval from HMRC (UK Customs). Having previously obtained AEO status should help the process, however the UK no longer requires guarantees for Customs Warehouses in Great Britain unless they consider there is a particular risk or need. Customs Warehouses in Northern Ireland still require a comprehensive guarantee under UCC rules as part of the NI protocol and AEO could be used to reduce or remove the guarantee required.
The approval process not only includes the physical premises for Customs Warehousing, which must be secure and the bonded area clearly defined, but the trader must also ensure they have sufficient records and visibility of the goods under the customs procedure at all times.
This is where a Duty Management System becomes invaluable.
Duty Management Systems: Streamlining Compliance
HMRC defines a duty management system as “a software package usually supplied by software suppliers to customs warehouse authorisation holders to support their commercial stock records. A duty management system will contain various modules to perform declaration procedures and/or stock accounting for customs warehouse and other special procedures. In most cases they will form part of the customs warehouse stock account as the data contained within them is critical to maintaining the audit trail and is usually the point of reference to the customs declaration of entry and discharge.”
Having a duty management system can take the effort out of maintaining the audit trail and ensure the data used on import/receipt can be automatically re-used on removal, whether that is to free circulation, re-export or to another customs regime.
Duty Management Systems ideally work in close collaboration with either the ERP or Warehouse Management System with integrations to support notification of removals and processing. Modern DMS solutions will be cloud based and offer APIs to send and receive data removing the need to have costly on-premise solutions with file based transfers or database connections.
Duty Management Systems should also be flexible in offering how goods are picked in the virtual warehouse: are they specific by goods location or lot numbers, or will there be some equivalence with smart picking ensuring the most duty-efficient position is taken? Smart picking is usually the case where it is decided the DMS should manage both bonded and duty-paid (free circulation) stock. However, this shouldn’t be mandatory if traders can segregate their stock in their own systems.
Simplified Procedures (CFSP)
Ideally traders should also seek to use Customs Simplified Procedures (CFSP). This allows traders to remove goods prior to submitting the actual declaration and wait for clearance. Under Entry in the Declarants Records (EIDR) authorisation, traders can merely record the details of the removal in their records (a combination of ERP/WMS and DMS) and submit the declaration at a later point but no later than the 4th working day of the following month. This means goods are not held for an indeterminate time pending customs clearance or potential inspections.
However, a DMS should also be able to handle non CFSP processes. Not only would this include exports but also scenarios where simplified procedures cannot be used or a company may decide they do not need that flexibility and are happy to hold removals for clearance.
Leveraging Customs Warehousing and DMS Integration
DMS can also be used where the stock belongs to multiple parties. This could be where there are different legal entities within a group such as a 3PL or 4PL where companies offer storage and distribution solutions for many clients.
Customs Warehousing can also work alongside Excise Warehousing for those importing and holding excise goods such as alcoholic goods; whilst Excise warehousing has its unique set of requirements being able to link the customs warehouse DMS to an Excise Warehouse solution provides traders with the ultimate flexibility.
A final benefit of Customs Warehousing is in combination with Authorised Consignee status to allow movements moving by Road under NCTS Transit procedures being received at the warehouse premises, discharged there into Customs Warehousing avoiding the need to stop at a Customs office or other approved location.